El Renacimiento a partir de la impresión 3D
Bicicletas, botes, armas y tablas de surf ya están empezado a salir de una impresora, en lugar de hacerlo de una línea de montaje. Y eso podría significar el acceso a mejores productos y más económicos.
Esta tecnología que ya lleva 30 años de existencia, está teniendo un increíble renacimiento. Durante los últimos meses, la técnica de fabricación vía impresión 3D, descolló en el mundo de la industria Outdoor, a pesar de su carácter – todavía – experimental. La innovadora tecnología de impresión 3D ya produjo artículos terminados, tales como un kayak y un sistema completo de suspensión para mountain- bike.
Ante esta evidencia, sólo cabe preguntarse: ¿cuánto tiempo pasará hasta que las bicicletas, botes y tablas salgan de una impresora en lugar de una línea de montaje? ¿Podría su próximo par de esquíes salir caliente de la prensa, tal vez luego de haberlo impreso en su casa con láminas de fibra de carbono, bordes de metal sintetizado por láser y con una orden de compra impresa, pegada en un extremo?, por supuesto!
Relacionada: Armas caseras en 3d
La impresión 3D -o, más exactamente, la fabricación aditiva – no es otra cosa que: la generación de un objeto sólido, tridimensional a partir de un archivo de origen digital.
Las técnicas de mecanizado o forja tradicionales crean objetos mediante fresado, corte o estampado de materiales hasta lograr su forma final. La inyección por moldeado depende, en general, de costosa maquinaria específica para cada pieza o producto.
La fabricación aditiva, por el contrario, imprime capas muy delgadas de un material de base para construir el objeto. Mediante el software apropiado, una impresora 3D y el material adecuado, se puede crear un número casi infinito de formas diferentes.
Las empresas productoras de artículos outdoor, han estado utilizando el sistema durante años, para producir prototipos y mock ups de exhibición, tanto físicos como gráficos, la novedad ahora es que cambia la función, lo que se busca es llegar al producto final.
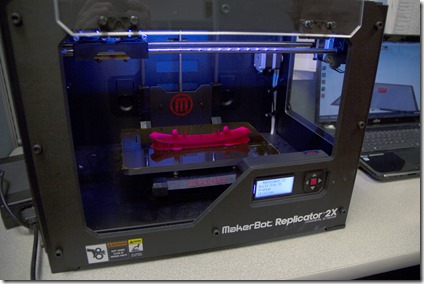
Confluente Watersports (la compañía propietaria de marcas de embarcaciones tales como: Dagger, Wave Sport y Percepción) utiliza la impresión en 3-D para diseñar piezas (manijas y empuñaduras) para someterlas a pruebas de uso en las embarcaciones, antes de que entren en producción a gran escala.
El Ingeniero de proyectos de Confluence, nos cuenta que hasta que la empresa comenzó a utilizar el método de impresión 3D, crear una arandela para una embarcación, requería de un complejo y burocrático proceso que involucraba la contratación de proveedores, matricería y muchos días de gestión hasta llegar al prototipo a probar. Desde la adopción de esta tecnología, la impresión del producto lleva sólo algunas horas, al igual que el montaje en la embarcación y la prueba. Por lo que el proceso puede iniciarse y finalizarse en el mismo día.
El gigante de los deportes de invierno K2 , utiliza la impresión en 3-D para comprobar el correcto montaje y ensamble de diferentes piezas y componentes de cascos y antiparras.
El fabricante de bicicletas Specialized utiliza la impresión en 3-D para una gran variedad de propósitos, que incluyen desde cuadros de bicicletas hasta repuestos para su propio túnel de viento (una herramienta indispensable en esa industria).
El Ingeniero en diseño de productos Matt Urquhart nos cuenta que la mayoría de los análisis aerodinámicos se realizan de forma virtual, a través del software (CFD) Dinámica Computacional de los Fluidos, pero ahora “con la impresión 3-D, las tres o cinco iteraciones del CFD, se pueden llevar al túnel de viento real, para ver cuál de los diseños propuestos es el más rápido”.
No son sólo las grandes empresas quienes aprovechan esta tecnología de vanguardia, Chris Williams, Director General de Empire Cycles , dice que en gran medida, el objetivo de la compañía de desarrollar su cuadro 3-D-impreso – el prototipo MX6 – fue para perfeccionar la fabricación tradicional. Nos cuenta que un proceso de diseño computarizado, llamado Optimización Topológica, les dio una forma eficiente para un elemento crucial en la performance de la bicicleta, el mástil del asiento del marco, que redujo su peso en un 40 por ciento. Así la impresión 3-D, les permitió hacer realidad a ese componente y probarlo antes de crear costosas herramientas para su fabricación definitiva.
Por lo tanto ¿llegará el día en que imprimiremos el marco de nuestra bicicleta en nuestro propio hogar? No está tan lejos como los coches voladores Jetson-esque, pero tampoco imaginemos que podremos, en el corto plazo, olvidarnos de la casa de venta de bicicletas. Lo fundamental es que existe la tecnología, dice Ping Fu, la Oficial en Jefe de Emprendimientos en 3-D Systems, la compañía que inventó la impresión 3-D en 1983, quien asegura que “la mayoría de los obstáculos no son técnicos sino culturales”.
Hace apenas una década, la impresión 3-D permitía sólo el uso de unos pocos plásticos básicos. Hoy en día, permite utilizar más de 100 materiales, no sólo plásticos, sino también metales y materiales compuestos. La bicicleta Empire se produjo a través de una tecnología llamada Selective Laser Sintering, donde un láser sobrecalienta metal en polvo (en este caso, Titanio) para fusionarlo, capa por capa, transformándolo en un objeto sólido. Recientemente la empresa MarkForged, asegura haber creado la primera impresora 3-D del mundo que puede imprimir formas en fibra de carbono de hilo continuo.
Pin Fu, también destaca que hay una gran oportunidad para la impresión 3-D en la personalización de los productos. Ella predice, que muy pronto se podrá obtener una exploración en 3-D del pie del cliente en un negocio de venta de equipos de esquí de alta gama, donde un “bootfitter”, utilizará la impresora 3-D para ofrecer una línea personalizada de botas de esquí. Ni que hablar de todo lo que se podrá ofrecer en la decoración gráfica de esquíes.
Pero los fabricantes a menudo se resisten a abandonar o desviarse de la producción tradicional debido, en gran medida, a las importantes inversiones ya realizadas en las fábricas.
El mercado de consumo está poco desarrollado, según Fu, porque la gente no está familiarizada con esa tecnología. La impresión 3-D no tiene ningún lugar real en el sistema educacional de los EE.UU. y debería tenerlo – asegura -.
Lee también: Un campamento de lujo en 3D
El Maker Movement, o sea el interés por querer hacer las cosas uno mismo, debería ser la principal motivación para alcanzar su conocimiento. “La comunidad educativa ofrece, potencialmente, un gran lugar para que la gente aprenda todo lo concerniente a la fabricación aditiva”, enfatiza Pin Fu.
Obstáculos culturales aparte, las dos principales barreras siguen siendo: el costo y la complejidad. El carbono básico utilizado por Mark Forged – impresora 3d capaz de imprimir carbono – equivale aproximadamente a siete veces el costo de su impresora de nylon. Y una impresora de SLS, que puede hacer un producto como los marcos de las bicicletas Empire, tiene un valor de mercado cercano a los u$s 500.000 – equivalente a 100 impresoras Mark Forged – (Empire acudió a un socio capitalista, Renishaw, para crear el marco).
Los costos de los materiales y las máquinas deberían disminuir, y, probablemente, lo hagan de forma rápida, pero en el futuro previsible, el rotomoldeado sigue siendo la forma más económica de hacer kayaks. Mucho más que la impresión 3D.
Relacionada: Las balas caseras en 3D
No obstante, la complejidad, termina siendo el factor más problemático. Las aleaciones metálicas a menudo deben ser tratadas térmicamente para alcanzar mayor durabilidad a largo plazo; un paso que no se puede dar, todavía, en la impresión 3-D-. El compuesto de fibra de carbono es un material complejo, utilizado en formas intrincadas, una instancia que las impresoras 3D todavía no dominan.
Un cuadro de bicicleta de carbono compuesto, puede contener hasta 500 láminas de fibra de diferentes calidades, dispuestas en el molde en una orientación y secuencia muy compleja y específica. A este proceso se lo denomina Proceso de Diseño – Layout Process – su complejidad requiere intenso trabajo y aún no ha podido automatizarse.
Andrew Juskaitis – Gerente mundial Senior de producto de la marca Giant, el mayor fabricante del mundo de bicicletas de carbono, asegura que: “Se podría producir – potencialmente – un cuadro de bicicleta razonablemente utilizable a gran escala. Pero todas las cualidades y atributos intrínsecos de un cuadro compuesto de fibra de carbono pueden lograrse sólo a través del Layout Process.” Y aún no hemos alcanzado ese nivel…”
En la próxima década, la impresión 3-D, sin dudas, crecerá y puede que llegue a sustituir a la fabricación convencional en algunas áreas. Ya es una realidad tangible hoy y una muy importante técnica de producción dentro, del área medicinal, por dar un ejemplo La Fabricación Aditiva, a diferencia de los autos voladores, ha puesto los cimientos para las grandes transformaciones. En este caso, se trata de algo que ya podemos ver, aunque todavía no podamos alcanzarlo.
Por: JOE LINDSEY
Traducida al español en exclusivo para Aire Libre por Carlos Nesci especial para AIRE LIBRE.
Fabricación Aditiva
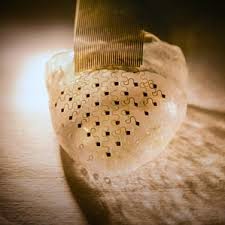
Soluciones Customizadas
Una realidad poética de la biología es que el corazón de cada uno tiene un tamaño y una forma ligeramente distintos al de los demás. Sin embargo, los implantes cardiacos actuales – marcapasos y desfibriladores – son casi de una sola medida. Lo que significa, entre otras cosas, que aunque estos dispositivos salven la vida de muchos pacientes, tienen limitaciones morfológicas y funcionales.
Dentro de los intentos por cambiar esta situación, los investigadores han creado un nuevo tipo de sensor de corazón personalizado. Valiéndose de imágenes del corazón de distintos animales, los científicos construyeron una maqueta del órgano mediante una impresora 3D. Después desarrollaron componentes electrónicos flexibles encima de la maqueta. Este material flexible se puede despegar de la maqueta impresa y colocar alrededor del corazón real para conseguir un encastre perfecto.
Esta tecnología permitirá desarrollar soluciones a la medida del corazón de cada paciente.
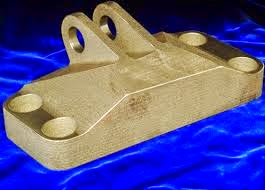
El 3D ya surca los cielos
Según la Gerente de Tecnología de GE, Christine Furstoss, la empresa está orientada a la investigación permanente de esta nueva tecnología que le permite agilizar procesos, ahorrar dinero e incrementar la performance de sus productos. Todo esto gracias a la impresión 3D, que si bien puede ser la palabra de moda de hoy en día, es en realidad sólo una fracción de todo el proceso de fabricación, pero también es el futuro y General Electric quiere liderar el camino hacia él.
El 3D Compañero de armas
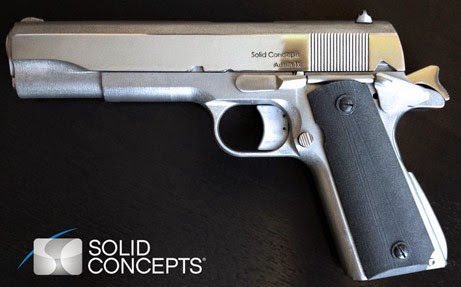
La misma consta de más de treinta componentes impresos en acero inoxidable 17-4 e Inconel 625, mientras que para la empuñadura se utilizó el Sinterizado Láser Selectivo (SLS). Las pruebas, de funcionamiento y precisión, demostraron que pasó con éxito un total de 50 rondas de disparos.
Para Kent Firestone, vicepresidente de la divisón manufactura aditiva de Solid Concepts, esta creación rompe con el prejuicio de que no se pueden hacer productos finales con la tecnología 3D. El sinterizado láser rindió examen y probó ser efectivo en la tolerancia a distintas fuerzas.
Eso sí, es un proceso complejo y costoso que debe estar en manos de ingenieros especializados y requiere de autorización gubernamental. Jamás podría imaginarse como un proceso hogareño.
Impactos: 199